Robots are not new technology. However, they are showing up in new places all the time such as smaller manufacturing and machine shops, medical settings, warehouses for packaging and order picking, and maybe even your local coffee shop!
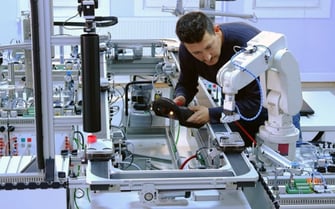
The trend is in smaller, collaborative robots that humans interact with directly in a work cell to add or remove parts, change tools, etc. As a result, few of us are surprised to see robots in new settings, but many of us are not used to working closely with them. We need to learn how to do our jobs differently and how to stay safe in the process. This blog covers the guiding principles of robot safety.
Risk assessment is critical
No two robots are used the same way, even for the same type of job. That means the safety risks and procedures are different in every application. An experienced integrator can help you anticipate safety problems and what will change when moving from manual to automated or robotic assisted work.
A formal risk assessment should be based on your application in your facility, not just generalities. Many of the dangers of manual manufacturing work persist in automated systems (e.g. fumes and burns in welding, cuts and abrasions from grinding/deburring). In addition, equipment like conveyors, turntables, gantries, and even safety gates or doors present hazards.
Also, not all potential risks are assigned the same priority. The severity and likelihood of potential injuries and the frequency of worker exposure to specific risks should guide prevention strategies.
The American National Standards Institute and the Robotic Industries Association standard ANSI/RIA R15.06-2012 illustrates the range of situations where risks occur:
- Actions of the robot under normal operating conditions and during teaching/programming, maintenance, setting, and cleaning
- Unexpected startup, power surge, or loss
- Access from all directions around machine/cell
- Accidental or intentional misuse of robot or tooling
- Computerized controls failure
Within the above situations are these factors:
- Robot payload, reach, operating speed, and path of motion
- End-of-arm tooling (e.g. sharp edges, pinch points, fumes, hot surfaces)
- Collision points where an operator’s path crosses with that of the robot
- Location of the work area relative to other hazardous areas and a workers’ ability to exit quickly if necessary
- Any continued movement due to inertia after powering off, and movement/lowering of overhead equipment when de-energized or de-pressurized
A safety strategy, like the equipment, must be custom
When it comes to safety procedures and equipment, “one size” doesn’t fit all situations. Fortunately, there are many mechanical and computer programmable devices to mix and match, such as:
- Laser perimeter monitors spaced and timed to keep people out until motion stops
- Light curtains
- Gates and overhead or sliding doors
- Interlocking switches to keep the next cycle from starting unless the switch is in the correct position
- Electromechanical guards and hinges, non-contact fiber optic switches
- Guard locking, which prevents a safety guard from being opened or removed
- Guards on exposed motors, gears, and belts
- Area scanners
- Redundant or combination safety systems (e.g. key lockout systems, two-hand power buttons)
- Power and force limiting robots with sensors (i.e. reduce speed or force when foreign objects or body parts are detected)
- Equipment with slower “collaborative mode” operation when humans are nearby
- Pressure-sensitive safety mats and personal protection equipment
Your integrator and internal design team should also plan a robotic work cell with adequate space around moving arms and identify and clearly mark danger zones in the vicinity.
Safety equipment and design aren’t failsafe
Cobots are often advertised as “inherently safe.” They’re smaller than their industrial counterparts, user-friendly, and easy to program and operate. And it can be easy to forget the serious harm they can inflict. Eye-catching design and colors don’t change the fact that a cobot fitted with a sharp or hot tool is still a safety risk, even when powered down.
Likewise, much safety equipment relies on programmable logic controllers (PLCs) that follow “if/then” computer logic. For example, if button X is pressed, then the arm rotates. Or, if the guard remains in an unlocked position, then the motor won’t start.
But, according to EHS Today, the Occupational Safety and Health Administration (OSHA) and others have noted that PLCs should not be viewed as failsafe. After all, it’s one computerized tool being used to keep another computerized tool from doing the wrong thing. Be mindful of possible errors/bugs in software, human programming mistakes, interference from electromagnetic or radio-frequency waves, and layers of equipment and controls that could interact in a way to counter intended programming. For example, consider what happens if an end-of-arm tool’s path crosses a safety beam and cuts power to another tool that’s suspended overhead and it lowers unexpectedly.
Safety training and compliance are fundamental
Operators, programmers, maintenance staff, engineers, and contractors will all have reason to get close to the equipment for various purposes. All must be kept safe while still having adequate access to the machinery to get their work done. That means training staff on safety equipment and procedures and in how to keep outsiders protected while working in your facility.
Tailor training to the role and work each group does. For example, maintenance doesn’t need to know details of programming the machine’s teach pendant, but does need to be aware of guards/gates, indicator lights, and all power connections to check before doing work in the area. And operators need more extensive training on switching out tooling than the engineering staff would.
Unfortunately, it’s not uncommon in manufacturing and industrial settings for employees to avoid or create workarounds for safety equipment. Inconvenient, overly complicated, or time-consuming safety systems make it harder to convince people it’s not worth the risk to skip a safety protocol “just this once.”
It’s hard to overstate how ingrained safety must be at all levels of the organization. Training makes staff comfortable working with the equipment and aware of daily risks, but developing a culture of safety in operations means everyone knows it’s just as important as proper component preparation or finished part quality.
While there are efficiencies and quality improvements to gain from robotics, nothing is more important than worker safety. At Force Design we can show you how to keep your workers safe while reaping the benefits of automation – give us a call!