For small to medium manufacturers seeking to boost production, create lean facilities, and stay competitive in their markets, automation is an increasingly viable option. Falling equipment prices, small and flexible cobots, and advancing technology are bringing automated manufacturing equipment into smaller facilities. What’s more, “factories that automate boring, low-paying jobs with high turnover not only stay competitive but can elevate workers to more interesting, better-paying jobs,” according to Cutting Tool Engineering.
If you’ve considered automating some or all of your manufacturing processes, you’ve probably thought about the decision between creating a customized system (usually with the help of an experienced automation supplier) and purchasing a commercial-off-the-shelf (COTS) package. Here are some things to consider when making that decision.
Custom vs. COTS
Sometimes “custom” automation is assumed to be prohibitively expensive, overly complicated, and out of reach for small to medium manufacturers. Because they’re generally built from scratch, custom systems require considerable time for non-recurring engineering (NRE), which adds to costs. Existing processes and applications must be reviewed closely and the integrator has to fully understand all of the needs and goals. There is often a lengthy prototyping phase in which processes are tested and debugged, and possibly redesigned. What’s more, once a system is built, if something goes wrong, some are uncomfortable being reliant on the few individuals who designed and built the system from a variety of components.
In contrast, COTS solutions are appealing because they may cost less up front. It can also be easier for a non-expert to visualize how components will fit together. The “plug and play” nature of some solutions (e.g. interchangeable end-of-arm tooling on a robotic arm) seems like an efficient way to add the specific functionality that’s needed without NRE. And for some, knowing that replacement parts, service, and support are available from the equipment’s manufacturer is reassuring.
But, as Corey Stefanczak notes in Control Engineering, “there are no COTS products that work purely ‘out of the box’ without any customization … This may involve writing scripts for supervisory control and data acquisition software, developing logic for a programmable logic controller, or writing custom communication components to bridge systems.”
If you’re thinking about a COTS solution, ask these questions:
- Does the component include features you don’t need but still must pay for (e.g. space for more inputs than you need)?
- Do you have the knowledge and expertise to configure, program, test, adjust, and maintain it?
- How long do you foresee the manufacturer supporting the model or unit you’ve purchased?
- What are your options if the unit is discontinued or if parts become hard to obtain in later years?
- If the manufacturer helped with initial set up, will they continue to support you over time?
- How expandable is a pre-packaged system, and how much can you tweak it to meet your changing needs?
- If your process requires flexibility, (e.g. changing weight capacity of parts or tools), can it meet that need?
- Will tweaks and changes end up making the COTS unit comparable in cost to a custom solution?
- To what extent does the COTS solution meet your needs and goals (or fail to)? For example, if it meets 80 percent of your needs and goals, are you willing to give up the other 20 percent?
- Do limitations of this solution create or compound inefficiencies in your processes?
- Can you anticipate any feasibility problems with the off-the-shelf system in the larger context up- and downstream and across departments? Do you have resources to overcome them (i.e. budget, time, space)?
Is Custom Automation Right for You?
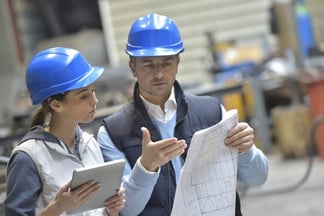
In the simplest terms, custom automation means building an exact solution for a specific need or problem. No two manufacturers use the same processes; therefore, a custom solution aligns with all of the unique aspects of your manufacturing to do precisely what you need it to do. Just like a tailor alters a garment to your exact measurements for the best fit, a custom integrator can make a system that fits your needs and applications.
“No two manufacturers use the same processes; therefore, a custom solution aligns with all of the unique aspects of your manufacturing to do precisely what you need it to do.” Tweet this.
You have a set of circumstances that are unlike those of others, even direct competitors. The resources that contribute to the kind and scale of automation you can use, like budget, physical space, availability of raw materials, employee skill and trainability, and time for implementation, training, and refining the new system.
Custom automation suppliers can bring expertise and experience with a range of applications to use these resources to your greatest advantage. They can also help you look at your existing set up in new ways. For example, creating a system from the ground up might raise opportunities to redesign a process or part to use raw materials cost-effectively, improve quality, efficiency, and reliability, or even to eliminate steps.
It’s also possible to design equipment with higher capacity or additional capabilities in anticipation of changes in the future, but the key difference from a COTS solution is that with customization, you get to decide which extras to include – they’re not part of the equipment unless you design them in.
Semi-automation is another custom approach to consider. Automation does not have to be an all-or-nothing solution. In fact, some applications are better performed by humans than with current technology (e.g. tasks requiring dexterity or human senses to do correctly, decisions made on the fly, or jobs with many or varied inputs such as differing part sizes or custom piecework). Still other applications are better suited to manual processes, whether because of lower volume, intricacy, or other factors. Examples of semi-automation include:
- Conveyors to move parts along quickly from person to person.
- Machines that feed blanks into press brakes with human operators .
- Cobots that position small parts to be welded by a person.
At first glance a COTS solution might seem less expensive or easier to implement than a custom-built one, but as we’ve shown, there are many factors in play. A side-by-side comparison of all the requirements, from set-up to debugging to long-term support, could change your approach to the project. If you’re unsure where to start, contact us to talk about your project – we can explore the options with you.
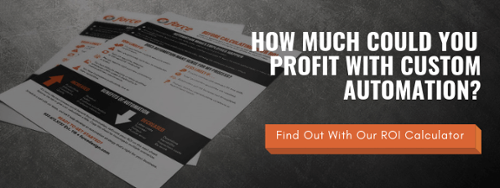