Automation in manufacturing isn’t exactly new but companies are finding new ways to apply it all the time. New and advancing technology including sensors, vision cameras, and collaborative robots (or cobots as they’re often called) expand possibilities from aircraft manufacturing to food processing and beyond. Across the board, flexible automation is a priority, along with worker safety and efficient production.
Here’s a snapshot of what’s new in four of the largest markets for automated manufacturing.
1. Automotive Manufacturing
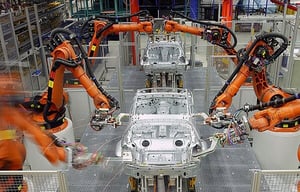
Companies routinely cite worker safety as a primary concern when considering automation. Power and force limiting robots are able to work side-by-side with humans, reaching across conveyor belts and moving throughout the facility without guarding or gates. It’s also possible for collaborative robots to switch between different programs on the fly so, for example, automation integrators can design in functionality that enables automatic ergonomic adjustments for each operator by entering a code or scanning a tag. It’s as quick and integrated into the workflow as automated tool changeover, and it keeps workers safe.
Flexibility and the ability to redeploy equipment as needed is also important. In this example from Universal Robots, a Nissan plant was having takt time overruns in several areas. They were able to use cobots outfitted with various tools to work with human operators and make up the losses. Because the cobots are easy to program it was possible to move them to new locations quickly.
Sensors have been used for years in automotive manufacturing, but improvements in the technology, combined with robotic arms and grippers, are expanding their use. For example, an arm can raise a component to the camera or move the camera around larger parts to inspect for damage or verify barcoded parts and trace components from start to finish. In both cases, images are taken and compared to reference points stored in memory to evaluate if a part is assembled correctly, matches a lot number, or other criteria. Sensors and cameras are also used in welding applications to sense seam locations and keep tools centered, both of which result in a more accurate finished product.
One change car companies may introduce is a move from conveyor-based production lines to flexible manufacturing cells. One reason is the increased complexity of vehicles like “smart” components, added electronics, and battery/alternative fuel sources, which add extra steps and different configurations to assembly. Another is the fact that these days most brands make several more models, and variations of each, than they did in past decades. As a result, different stops along the line can take vastly different amounts of time.
“Increasing complexity makes it difficult to balance process times across all workstations, because some workers will finish their assigned tasks before the conveyor belt moves on. This imbalance in worker utilization results in unproductive time on the belt,” according to this article from Boston Consulting Group. The “interconnectedness of conveyor belts limits opportunities to adjust the production sequence in order to reduce takt time losses.” With a modular cell format, a vehicle only goes to the ones relevant to its assembly or parts and tool changeover for different models or trim lines is automatic. Production metrics are based on the process time of the task done at each cell instead of the takt time for the whole vehicle to move through line, which makes sense as product variance increases.
2. Consumer Products and the Food and Beverage Industry
Throughout your home or office there are probably few items that didn’t involve some type of automated manufacturing, packaging, or handling on its way to you. And it’s not just about appliances or electronics anymore. Food companies look to automation equipment for a growing range of tasks too.
Assembly, especially when small components or tedious steps are involved, is easier to automate in many consumer goods thanks to robots that are small enough to
mount on a tabletop and highly dexterous, hand-like grippers. One example is these robots that assemble key fobs. Programmed to follow the same path repeatedly as the carousel of fobs moves by, they can transform what was a monotonous job putting tiny parts together into the higher-level work of managing throughput of the entire workstation.
Kitting, where sets of products or components for later assembly are packed into a container, can also be automated by organizing components on carousels, movable racks, and lifts, for a robotic arm or autonomous guided vehicle (AGV) to retrieve and package.
Food handling applications like packing fruit and vegetables and even depanning muffins is possible thanks to end-of-arm tools like vacuum cups, soft grippers, and forks. Made of food-safe materials and with easy-to-clean designs, robots can reduce time spent packaging delicate items.
Vision cameras are also used for verification of kitted items’ orientation, placement, and quality. In food and beverage applications they can check seals, verify barcodes and lot numbers, and monitor fill lines, notifying an operator of problems and simplifying traceability. A robot camera just might check that your next box of chocolates is packed according to the flavor chart in the lid!
3. Medical Devices and Products
In low volume, high mix medical manufacturing it’s important to maintain product consistency. Robotic and computerized production equipment is known for its ability to do the same task over and over with high precision, as is seen in this robotic syringe assembly cell. And because most are easily programmed on-the-fly, operators can quickly change from one product to another with minimal delay in production.
The key is to understand the manufacturing process and anticipate the variants of a part or component so flexibility can be built in. Features like automatic tool changeover, teach pendants, and easily adjusted fixturing mean the same arm can work on an array of related products within a single day or shift.
As in other industries, vision guided systems improve accuracy and reduce the tedium of kitting (e.g. putting items into blister packs), pick and place or sorting, and product verification. By redesigning the workflow for tasks like this dental crown milling process, a vision camera helps the automated pick and place arm load and retrieve crown parts more quickly and frees human workers to do other tasks around the dental lab.
Material handling application like autonomous guided vehicles (AGVs) can save time in pharmaceutical and medical product facilities, especially in cleanroom environments, where donning and doffing protective clothing every time something is needed from outside the area is inefficient. These robots can deliver items like specimens, samples, and supplies on demand instead of only at one or two scheduled times during shift changes.
An emerging application in laboratory environments is sample preparation for drug discovery. The accuracy and repeatability of computers and robots means arms can inject samples in test tubes and perform other menial tasks, freeing technicians to oversee the process or tend to additional tasks.
4. Aircraft Manufacturing
Drilling and filling holes (with rivets or screws) is a significant part of constructing an airplane and this is where automation has traditionally been used, often with large, gantry-mounted equipment. Due to the size of most aircraft, assembly line production and smaller robots just aren’t feasible. Tools and equipment must be brought to the aircraft instead of moving it from station to station.
What’s more, “the immense importance of safety, coupled with strict regulations, inspires a conservative approach,” so adopting new techniques and equipment has been slow, according to the Robotic Industries Association.
Compared to other industries, aerospace assembly is complex and low-volume, and involves large numbers of unique operations to produce relatively few final products. Despite the challenges, many manufacturers have a large backlog, especially in commercial aircraft, and need to find ways to use automation.
Drilling is one example. “Conventional drilling has issues with high on-axis reaction forces and levels of vibration. This makes it difficult for the relatively flexible structures of industrial robots to produce good-quality, accurate holes,” according to Dr Jody Muelaner writing on Engineering.com. Orbital drilling is one solution because it uses a smaller machine “light enough for a robot to handle, enabling flexible and reconfigurable drilling within large assemblies.” It can be positioned similarly to a conventional drilling machine.
Another example is surface preparation and painting. “The beauty of putting paint on an aircraft’s fuselage with robots is there’s a material savings of between 30 to 50% by doing it robotically, and that also means a 30–50% savings in weight as well,” says Chris Blanchette, Manager of Aerospace Automation at FANUC America Corporation. He notes it is critical to have dispensing tools to go on the robot to ensure there are no gaps in the fuselage for proper application.
Much attention is being paid to human-robot collaboration. For example, material handling robots are being used to hold large parts in place during assembly, and pick and place robots are used for kitting smaller components used in assembly. These “solutions allow the highly skilled labor that is found within the aerospace industry to continue to perform the required craftsmanship while allowing the robot [to] perform the unwanted/unskilled tasks,” says Dan Friz, Director of Business Development for KUKA Systems.
Manufacturing technology is always changing, and thanks to automation, companies are finding more and more ways to boost efficiency and quality while keeping workers safe and productive. The factory floor looks different than it did even ten years ago, and ten years from now AI and Industry 4.0 (or its successor) will have ushered in even more changes. We’ll keep you up to date on the latest trends and capabilities – contact us to learn more.