According to a 2016 survey by the MAPI Foundation and Rockwell Automation, the top reason companies said they chose not to automate is that perceived return on investment (ROI) did not justify the initial cost of purchase and implementation (47 percent). If this reasoning resonates with you, ask yourself if you’re looking at ROI comprehensively when considering automation.
Automated systems, from conveyors to cobots, welding machines to vision cameras, allow you to approach your processes and labor distribution in new ways. Those changes, in turn, boost revenue and create savings that offset the investment. But you can also take a broad view over the long term to see just how far-reaching the effects of automation are. Keep reading to see how the benefits of automation can increase your ROI, and over time, your bottom line.
The Direct Monetary Value of Automation
Many of the changes that result from automation are directly observed and easily expressed in monetary terms. For example, if your hourly production rate increases, possible results include higher sales or the ability to fill larger orders. As a result, your revenue increases, which helps directly offset the cost of the new equipment and accompanying expenses.
But by taking a broader perspective, you can uncover more efficiencies and improvements exclusive to automated processes. These automation “side effects” are more likely to generate savings than direct revenue, but they still contribute to ROI.
One example is higher precision of the equipment, which can lead to reduced waste and fewer scrapped parts. Precision is also linked to more efficient use of raw materials and consumables.
Another example is gaining the ability to closely control inputs and processes. The result is often “increased throughput by being able to operate closer to production limits (control optimization). Throughput gains might also come from shorter batch cycle times, lower grade transition time, less product re-blending, and decreases in scheduled shutdown duration and frequency,” according to Control Engineering.
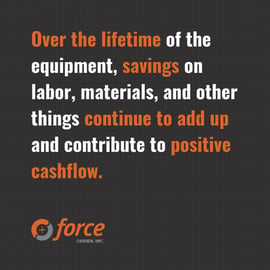
Benefits like these come into play almost as soon as the new system is up and running, but they continue for the life of the equipment, long after the break-even point. Automation expert Ron Potter suggests that rather than focus only on the first couple of years, you’ll see even more monetary
value over 10, 15, or more years. For example, looking at a robot as a source of inexpensive labor, you’ll
save money on things like lost production due to breaks, sick time, vacations, and injuries. You may also save on training and insurance/benefit costs and workers compensation. But even after labor savings have helped make up for expense of equipment, those savings continue as long as you keep using it.
Over the lifetime of the equipment, savings on labor, materials, and other things continue to add up and contribute to positive cashflow.
Don’t Discount Intangible Benefits
The value of automating some or all of your facility also plays out in ways that are not immediately visible. Even benefits and opportunities that are harder to quantify in dollars contribute to ROI, savings, and revenue indirectly. Examples include:
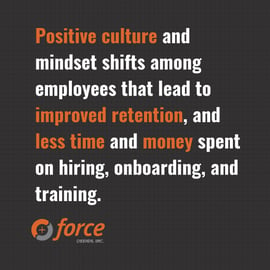
- Positive culture and mindset shifts among employees that lead to improved retention, and less time and money spent on hiring, onboarding, and training. Employees may feel increased job satisfaction from working with modern equipment, appreciate the ability to work to an older age due to lighter physical demand and better ergonomics, or enjoy a switch to higher-level tasks.
- Opportunities to update and tweak old workflows and procedures that boost efficiency by eliminating repetition or redistributing staff.
- Computerized and “smart” machines that track data, making it possible to measure production closely, find and fix problems quickly, and adjust to customer demand in real time. All of these help you stay competitive and flexible in your market.
- The ability to reconfigure or reprogram equipment for future needs, reducing future capital spending, minimizing training costs for new machines, and extending the useful life of the equipment to new areas of production.
- Built-in instrumentation or software for “asset health monitoring,” which helps you catch problems before they require an overhaul or
total replacement, monitor wear and tear, and make adjustments over time instead of running
a machine until it fails (a good, ongoing
relationship with your automation vendor is another great way to accomplish this!). - Appearance of the equipment and the sense of
a modern, high-tech “look and feel” of your
facility, which can give a competitive edge in winning customers and employees.
Even though none of these are direct results of faster cycle time or error reduction, they impact your company’s ability to save money and use resources to your best advantage.
Of course, every company and every automation project is different, and returns vary. But, hopefully we’ve encouraged you to take a more comprehensive view of ROI as you consider custom automation for your facility. If you’re not sure it’s the right choice for you, we’d be happy to talk with you about options – please contact us!
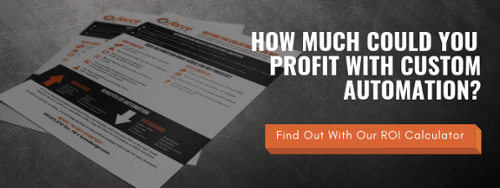