Collaborative robots, nicknamed cobots, are the more accessible, approachable descendants of traditional industrial robots. They’re smaller, less expensive, and, thanks to intuitive software, easier for non-experts to program. Built-in safety features expand the types of jobs they can accomplish and allow them to perform complex operations side-by-side with human workers. They can even be reprogrammed to switch between tasks in the same facility, making them flexible and cost-effective. It’s time for manufacturers who thought robotic automation was out of reach to revisit that assumption. Is a cobot right for your company after all? Read on for the facts you need to decide.
Evolution of Robotics
What do you imagine when you think about robots in manufacturing? There was a time when industrial robots fit the stereotypical image of a towering mechanical arm, perhaps equipped with a welding tool or pincer, enclosed in a fenced area. Most likely that machine was doing a job considered dangerous or physically prohibitive for human workers, and it was definitely working at a distance from them, in isolation.
Early manufacturing robots were made for fixed use, designed to make one part or to complete one task until that part or job no longer was needed. Then it was time to get a new machine. The capital investment and physical space required for such dedicated machinery put early robots out of reach for all but the largest industrial companies.
Things have been evolving continuously ever since the first robots were introduced in automotive, aerospace, and packaging/shipping facilities.
To be sure, large-scale industrial robots still exist and are in use around the world today. But designs and capabilities have continued to change. Today, thanks to advances in controls and actuators, safety features, sensors, and computing power (not to mention shrinking component sizes and costs), new types of robots are capable of working near and with human coworkers in a wider range of settings. Consider the following:
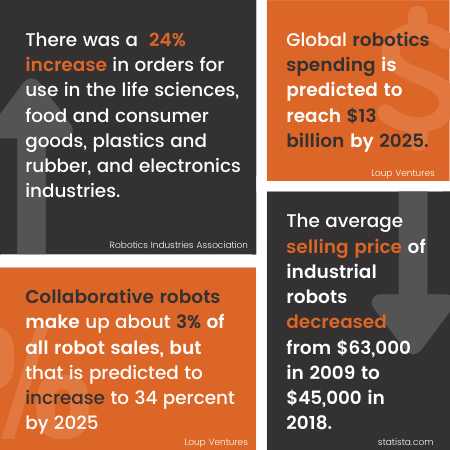
- Global robotics spending is predicted to reach $13 billion by 2025, according to research by Loup Ventures
- The average selling price of industrial robots decreased from $63,000 in 2009 to $45,000 in 2018, according to statista.com.
- Collaborative robots make up about 3 percent of all robot sales, but that is predicted to increase to 34 percent by 2025, according to Loup Ventures research.
- According to the Robotics Industries Association, although fewer units were sold in 2018 overall, there was a 24 percent increase in orders for use in the life sciences, food and consumer goods, plastics and rubber, and electronics industries.
What are Cobots?
Traditional industrial robots are built and programmed to do a single task at a distance from workers on the manufacturing or assembly floor. Common types include articulated arms, wheeled mobile robots, and gantry/rectilinear models, and they are often used to process large batches of single items: welding, drilling, spray application (paint, adhesive), transporting items across an area, loading and unloading heavy items. They are large, heavy, fast, and very strong, all of which make them hazardous to humans and require them to be surrounded by fencing or other barriers. Because they operate independently of the people around them, traditional industrial robots work in parallel, not in collaboration.
In contrast, a cobot is, according to its patent (US5952796A), “an apparatus and method for direct physical interaction between a person and a general-purpose manipulator controlled by a computer.” The key words here are direct physical interaction.
Collaboration is defined less by the task performed than by the features of the robot that make it safe and helpful for working side by side with humans. Machine and person can work on the same task, assembly, object, or activity at the same time in the same physical area, such as a work cell, station, or work bench.
There are several types of collaborative robot available “off-the-shelf,” which means there are options to suit a range of needs. Most cobots can also be customized and integrated into manufacturing production systems with accessories and tools like vision cameras, suction cup grippers, and welding tips (check out this example from Universal Robots on the right). Gone are the days when the only option for a robotic arm was to build a large, dedicated machine from scratch.
In stark contrast to older-style robots, bolted to the floor in a cage, collaborative models can be mobile multitaskers. They’re small and lightweight, able to be moved around the manufacturing floor or facility. Once in their new destination, easy and intuitive GUIs allow operators to quickly switch between tasks. Many models can also be programmed for new operations by hand guiding the arm through steps at the point of need. This flexibility is helpful for small and medium-size manufacturers, especially those in high-mix/low-volume and just-in-time (JIT) settings.
Cobots come in a range of sizes, payload capabilities, maximum reach distances, and operating speeds. Most are compact: small enough to mount on a workbench or sturdy cart. Larger models can mount to the floor (or ceiling, or wall, depending on the application). Payload limits are generally between about 3 and 16 kg (6.6 to 35.3 pounds), though FANUC has developed one that can lift up to 35 kg (just over 77 pounds). Typical reach ranges from 500 mm (19.7 inches) to 900 mm (35.4 inches). Where traditional industrial arms can move as fast as 3 meters/sec or more, most cobots have a maximum of speed of 1.5 m/s, though they’re usually operated at 1 m/s or less, depending on the proximity to human coworkers. Many also use six-axis motion, allowing for sophisticated movement around and between other equipment.
Another distinguishing feature cobots share is built-in controls to enhance safe operation. These include programmable settings to create “zones” of faster or slower speeds, collision avoidance, and sensors that stop the machine when a hand or other object enters an unanticipated area. (We’ll cover details about safety features in the next section.)
Along with safety, ergonomics can be improved with a cobot assistant. This is especially relevant as workers age, lose dexterity, and feel effects of standing, lifting, or twisting earlier in a shift. It also offers options to broaden the range of abilities and skills needed to perform a job, such as programming the robotic arm to do a task, making adjustments to settings based on computer data, or performing a job while seated. With these capabilities you can grow your manufacturing workforce.
Rather than removing human workers from jobs entirely, cobots usually integrate into the portions of a process that are repetitive or dull enough to risk errors or injury. Their small size and dexterous movement mean they make great assistants for tasks with small parts or intricate placement – the types of jobs humans do at workbenches and on the manufacturing floor. Examples include:
- pick and place (e.g. moving item from conveyor to tray)
- machine tending (e.g. injection molding or CNC machines)
- packaging and palletizing
- process tasks, when equipped with end effector tools (e.g. gluing, drilling, welding)
- finishing (sand, polish, deburr, trim)
- quality inspection, when equipped with a vision camera
- assembly
- dispensing (e.g. adhesive, lubricant, sealant)
- painting, coating, dipping
As accessories and technology evolve, applications are growing in other industries such as agriculture, food service, medical and more. With each new way of using cobot technology, the tasks that make up a person’s job will change, but there will remain aspects of the work that are not done by automation equipment. Universal Robots provides several examples of this collaborative work in action on their website, including this injection molding machine tending example on the left.
A final difference to consider between traditional industrial robots and their cobot cousins involves return on investment (ROI). Cobots are less expensive than their large-scale industrial cousins because they’re smaller and often require less technical expertise and time to install, program, and maintain. Many models cost under $40,000, though there will likely be additional costs for tools, accessories, or grippers for customizing it to the task at hand. Another initial investment may be the choice to work with an automation integrator to help efficiently integrate it into your manufacturing processes.
It’s possible to see the direct impact of the cobot within a period of months. For example, when a cobot increases your hourly production rate, results may include higher sales or the ability to fill larger orders. As a result, your revenue increases, which helps directly offset the cost of the new equipment and accompanying expenses. Indirect influences on ROI include reduced downtime due to worker fatigue or injury, opportunities to review existing workflows for inefficiencies, and, identifying additional work cells or departments in which to redeploy the cobot. All of these contribute to time and monetary savings and to ROI.
Cobot Safety and Risk Factors
Collaborative robots are often billed as “inherently safe.” This usually refers to the built-in safety features most collaborative robot designs have that make them more safe than traditional factory robots. The focus is generally on how these robots can be used without caging or fencing or include rounded edges and corners.
ISO 10218 provides general information for robot designers and manufacturers in creating robots that can work safely with humans. More specific guidelines have been provided in ISO Technical Specification 15066, which was updated in 2016 to reflect the state of the art and current technology.
ISO/TS 15066 describes four major capabilities that render a robot collaborative in terms of ensuring human safety:
- safety monitored stop (i.e. when something triggers the robot’s programmed safety parameters, the robot stops until it is explicitly told to start again)
- hand guiding for programming and “teaching” a sequence of steps (safeguards must be in place so that hand guiding only occur under certain conditions: when the robot is stopped, when speed and force limits are in place, when the operator has selected hand guiding mode, a.k.a. positive confirmation)
- speed and separation monitoring (i.e. sensors are installed to track where a human is, and safety zones can be programmed so the robot operates at a certain speed within each zone)
- power and force limiting (including sensors that reduce the speed and force applied if a potential collision or force overload is detected; also design elements like rounded corners to dissipate forces on impact and ways to add sensors to robotic arm joints)
“One of the central ideas behind ISO/TS 15066 is that if contact between robots and humans is allowed, and incidental contact does occur, then that contact shall not result in pain or injury,” notes an article on risk assessment from Engineering.com. Part of this means defining pain and injury, as well as identifying safe maximum operating speeds, and core robot capabilities to avoid contact.
Sensors are one of the primary ways collaborative robots are able to achieve safety guidelines and capabilities. Common types of sensors include:
- grippers with tactile sensitivity (i.e. to “feel” the what is being touched and adjust grip if necessary)
- accelerometers to detect bumps and nearby movement
- 3d vision cameras to detect objects
- lasers to trigger an action when breached (e.g. stop moving, reduce force)
- force-torque sensors
- current feedback sensors
So are these machines truly safe? In many ways, the safety guidelines and technology described do make these robots far safer for close, regular contact with human coworkers. However, safety is also contingent on what the robot is doing. An often-cited example is a cobot with a sharp end effector like a knife. All of the latest safety features and sensors can’t change the fact that a sharp tool is a hazard.
Unfortunately, there are still many ways to be injured if application and operation are not planned and assessed carefully. This doesn’t mean cobots can’t use sharp or dangerous tools, but it does mean additional safety assessment and planning are necessary.
Robotic accessory company Robotiq suggests studying each of these when conducting a risk assessment of a particular task:
- Severity of injury
- Possibility of injury occurrence
- Possibility of injury avoidance
- Frequency of exposure to risk
The Robotic Industries Association (RIA ) gives several detailed examples to help you understand exactly what the risks are for a task and how likely or unlikely they are. For example, as you review what the human and robot will both do in a given situation, consider risks of pinching, crushing, or pinning of a body part between the robot’s arm and wrist, between the gripper and part, between the part and fixture (the object against which the part rests or is held), or between the robot and other nearby structures (e.g. wall, movable cart, chair, table).
It’s important to look at all the components of a task, such as loading a tray. When broken down, steps might include gripping an object, lifting it, moving it a programmed number of inches by turning/rotating a set number of degrees, lowering the object, releasing it, and returning the arm or gripper to the starting point. In addition to the primary operation, consider any hazards involved in other tasks such as maintenance, cleaning, changeover, or transporting the machine.
Implications for Workers
The promise of collaborative robots and other automation is a combination of efficient production with safe, user-friendly equipment. Planned and implemented thoughtfully, they can transform your manufacturing processes. But the machines also have an impact on workers and jobs that can’t be ignored.
Currently manufacturing and other industries face a skills gap in which there are more open positions than workers qualified or willing to fill them. Main drivers include:
- The large Baby Boomer generation is retiring faster than openings can be filled.
- Younger workers are spending a longer time on their formal education and entering the workforce later, often in traditionally professional positions such as engineers or managers and not manual, factory, and industrial jobs.
- Advancing technology means a host of new skills is required to work with the equipment, which many existing factory workers lack or cannot readily obtain.
- Manufacturing continues to suffer from a powerful, if outdated, image as dirty, dull, and dangerous and, therefore, doesn’t appeal to enough young workers.
Robots and automation equipment can offset the skills gap to a degree by performing some of the tedious, dangerous, or unskilled tasks. It’s not hard to imagine a futuristic factory with robots at every workstation and no human beings in sight. While automation can eliminate some of the less desirable positions that go unfilled when older workers retire, it’s not a complete solution. The current reality, especially for small to medium-sized businesses, is humans and robots have a complementary working relationship.
This is partly due to production lines and work cells redesigned for robotic arms, and partly due to the type of work automation generates. Programming, engineering, and systems integration, and IT work are critical to keeping electronic automation equipment up and running. Even as artificial intelligence and machine learning work their way onto factory floors and industry 4.0 promises to take production to new levels of efficiency, humans are still very much a part of automated manufacturing. The trick is finding workers with the right skills for the jobs.
The traditionally “blue-collar” positions typical to manufacturing also start to look different as factories integrate collaborative robots. For example, skills like computer literacy or hand guiding a robotic arm through a new sequence may replace manual machine tending and simple pick-and-place tasks.
Experts disagree on exactly how many jobs might be lost completely to robotics and automation and how many will persist but with major changes. But there is agreement that manufacturing workers won’t be able to get by with just the skills they have now. Retraining current workers to program and manage computerized equipment is one of the keys to retaining employees. Likewise, students in training programs and technical schools need access to the latest technology so they have skills employers need.
If you’ve considered introducing cobots to your facility, you might see these changes in the nature of work:
- Robotics can enable workers to stay on the job later in life. Safety and ergonomic features most cobots incorporate can offset changes in strength, dexterity, grip, coordination, and response time that naturally accompany the aging process. It means financial security for them and a filled position for you.
- Enhanced safety and ergonomic features make jobs accessible to some workers with disabilities, opening new work options for this historically underemployed group.
- When the tedious or dangerous tasks are automated, jobs can be redesigned to give operators a higher quality of work (e.g. adjust computerized controls, oversee bank of machines, troubleshoot and program, assess production, and make recommendations). It’s more interesting for current employees and more appealing to job seekers.
- Machine operators, accustomed to pacing themselves to endure a physically-demanding eight-hour shift, must adapt to a new form of uptime: keeping the machine busy the entire shift. Sharing the workload with a new machine often results in creating opportunities for monitoring and managing equipment, analyzing production data, and other higher-level work. You might even notice higher job satisfaction and improved morale as a result.
- Continuous education, sharing knowledge, and familiarity with computerized tools may become valued parts of your company’s culture.
Types of Cobots and Applications
It would probably be difficult to find two manufacturers using a collaborative robot in the exact same way, even for similar parts or processes. How they’re deployed for a low-volume/high-mix contract manufacturing environment differs greatly from use in a packaging facility or spray-painting department. The unique, often proprietary methods in this industry are a good match for the adaptability of cobots.
Because most cobots are small and can be equipped with a range of tools for different jobs, programmed with user-friendly interfaces, it might seem like the easiest solution is to purchase one and use as a “plug and play” piece of equipment to make some tasks more convenient. This is a viable option thanks to commercial off-the-shelf (COTS) products available from many manufacturers.
Depending on the application and if you anticipate moving it around your facility to support human workers in a number of work cells or departments, this can be an excellent option, especially when taking your first steps into automation. Just keep in mind even off-the-shelf models will still require some initial set up and selection of the proper size, end of arm tools, and other accessories.
If you’re ready to go all-in with robotics, working with a vendor to integrate cobots into your manual processes can be a great way to examine your setup as a whole system. It’s an opportunity to find areas for improvement or adjustment and make physical changes to the layout to get the most out of one or more cobots. An integrator’s expertise and experience with collaborative robots in variety of settings can be an introduction to applications you hadn’t considered, and accessories and features you didn’t realize exist.
Fitting In: Finding the Right Place for a Cobot in Your Facility
Your workers have probably already thought “I wish I had a machine that could do this task for me.” If you haven’t already heard these musings from them, just ask. They’ll probably be able to come up with a few ideas for making their work less tedious, physically demanding, or more fulfilling.
Observe your process with an eye for what can be automated – online videos and robot vendor websites are a great way to see cobots in action and get a sense of all the things they can do. Can you picture it in your building alongside your employees? Brainstorm and have fun imagining what could be, such as:
- assembling pieces then rotating them into position for a worker to complete the job
- opening the door to a CNC machine, inserting an unfinished piece of material, closing the door, and repeating the process to remove it after machining
- inserting or removing items from the appropriate tray or rack based on simple logic programming
- tending an injection molding machine, opening and removing the part, pressing the start button, then trimming the new part while the next is molded.
As you perform a close review of your processes and workflows to identify areas where cobot might make a difference, trace any problems up and downstream to find root causes. These may be some of the best opportunities for automation. Things to pay attention to include:
- Time-intensive steps (e.g. waiting for material to come up to temperature, time for parts to queue, etc.) – especially if an operator could be working on something else during this time
- Tasks that require multiple operators
Routine quality problems like a frequent need to scrap or rework, or areas of inconsistent quality between operators
- Points of wasted labor or labor that is better spent on “human-only” tasks (e.g. installing delicate electrical wires or soldering tiny components)
- Consistent bottlenecks and backups in production
- Work that utilizes heavy tools or parts – especially since these often cause workers to slow down as the shift progresses
- Rule-based operations (e.g. sorting, simple if-then logic)
- Tasks that don’t rely on human senses to complete (e.g. process that can only begin once paint/adhesive is dry to the touch)
- Jobs or locations in your facility with a record of accidents or near misses
- Jobs employees complain about, dislike, or find challenging
- Areas with exposure to gases, dust, or byproducts of the manufacturing process
- Activities with repetitive motion and ergonomic problems, especially over time and repeated exposure
- Tasks requiring prolonged, intense focus or constantly shifting attention
It’s challenging to review long-standing processes, but try to observe operations with fresh eyes to identify risks that may have gone undetected. Just because you’ve always done something one way doesn’t make it the best option. Automating a process is not merely a one-to-one substitution where a machine is swapped for a human. It can include changes to the order of steps, operator tasks, materials used, and even other processes up- or downstream. Adding a cobot can alter entire processes, or even the parts being fabricated, which may be redesigned for greater efficiency, production or quality.
How to Prioritize When There are Too Many Choices
In general, the greatest opportunities for collaborative robots are where you need a reduction in time, labor, movements, steps, or even costs of consumables (e.g. weld wire, glue, paint, fasteners). Knowing which area is most important to reduce can help narrow the options. Or put another way, what’s the impact of not making a change in each scenario?
But what if you find a dozen potential uses for a cobot? What if you end up with more questions than answers?
Start by stating your goals for adding a robot, and be specific. Do you want to test whether a certain task can be done by a robot? Is this a test case for future additional automation in your facility? How will you quantify goals and measure success? Examples could be a 15% reduction in scrap materials, 100% fewer injury accidents, or a measurable increase in revenue tracked to production gains from automation.
Also consider available resources: time, money, training, existing workers and their abilities to learn new skills, space to rearrange and add equipment. If you’re overwhelmed with options, speaking with a reputable automation integrator can help you sort out the possible from the impracticable.
Automation is not all-or-nothing but can be combined with manual work (e.g. a robotic arm with a gripper that lifts and feeds a blank into a lathe or positions a small part to be welded by a person). You can also develop a scalable cobot plan: start by automating one simple task and build in ways to expand it’s use in other departments or work cells in the future. Most cobots can be used with a variety of grippers and tools for maximum flexibility, and they’re often quick and easy to program by hand-guiding or a straightforward HMI.
Tools And Accessories
As we’ve explained above, due to size and safety features, cobots can be used in a variety of settings. What actually gets the job done and customizes the cobot to the task is the combination of tools, accessories, and computer connectivity (that is, the ability to communicate with the machines from a central control room or offsite location with updates to software or programming). This is what gives manufacturers and integrators an array of creative ways to mix and match current technology and plan for emerging capabilities. The technology won’t stand still, so here’s the current view.
Tools/End Effectors
Selecting the right tool means thinking about what the machine is doing with the part in question (e.g. assemble, position, pick up, cut) and what actions need to happen (e.g. open a CNC machine door or push a button). This points in the general direction of tool category, such as:
- Welding
- Material removal/finishing (e.g. trim, sand, deburr, polish)
- Gripping (e.g. pincer, fingers, various configurations and materials of fingers)
- Vacuum for lifting delicate or flat pieces (e.g. cup or bellows)
Look at the whole picture when selecting tools, including the shape and size of the workpiece, payload limits, target cycle time, and actuators. All of these are interdependent. “For example, taking advantage of the arm’s maximum payload will mean that the robot will have to move at a slower speed. Heavier parts also require the right gripper selection to reduce the risk of accidental dropping.” See our blog post on end-of-arm-tooling, or EOAT, for more.
Some cobots come with tooling kits and the ability to switch out tools to quickly redeploy them for other jobs to maximize flexibility. Programming and changeover are designed to be intuitive and clear with a limited number of options to control programming outcomes. Operators cannot control everything about the machine from their HMI panel, only the features required to sync a new end effector and “teach” the cobot. A further advantage of this simplified yet effective programming is not losing efficiencies gained with the cobot to extra time dealing with a clunky or confusing interface.
Accessories: Sensors and Vision
Cobots are outfitted with many types of sensors, but force/torque and laser sensors are among the most common. Force/torque sensors help maintain safety and keep the machine performing its job correctly. By measuring changes in applied force and rotation, they can:
- assure constant pressure in applications like sanding and polishing
- stop on impact to prevent further damaging force by monitoring the motor’s feedback current (i.e. hitting an object creates measurable force in opposition to the motor’s rotation)
- monitor probe deflection and contact pressure while measuring a part during quality inspection
- learn to follow a particular path with hand-guiding
Laser sensors project a beam of photons that, when broken by an object, indicates the presence of something like the corner of a part or a reflective surface. A simple way to visualize this is to think of what happens when you place your hand in front of a laser pointer: your hand stops the beam. A laser sensor uses that feedback to calculate the presence of an object (i.e. your hand). Some applications include:
- collision avoidance by stopping the robotic arm or tool when an object breaks the beam
- mapping/positioning a tool (or the robot itself in the case of a mobile robot) relative to an object
- determining size and shape of an object by reading tracking points (e.g. corners, edges)
- determining color or metallic qualities by measuring the amount of energy reflected back from an object in the beam’s path
Depending on your application and requirements, you can install other types and combinations of sensors such as accelerometers, GPS, ultrasonic range sensors, or temperature sensors.
Two-and-three-dimension vision cameras are another way a cobot orients itself and its tools in space. More cameras generally mean more angles and vantage points (and more visual data and feedback for the machine), but not all applications require vision capabilities. Operations such as sorting or pick-and-place that require a robot to visually identify parts and confirm sorting criteria often benefit from camera systems. However, tactile sensitivity in the form on force/torque sensors may be sufficient for a gripper to “know” when it is holding an object.
Connectivity: Internet-Enabled Machines, Remote Access, and Smart Electronics
Cobots and other automation equipment rely on electronics to run logic controllers that govern movement, gather data from sensors, and store and recall paths and movements. Connecting a robot to your local area network (LAN) or a VPN online allows for two-way data transmission to optimize operations. For example, remote access to a machine can push software upgrades, update control panel screens or add new capabilities for operators.
Your engineers or automation vendor can also accomplish complex reprogramming and troubleshooting from their location before making a trip to your facility. Maintenance staff can use production data (e.g. temperatures, cycle times, number of cycles) to monitor the condition of a machine and its components to predict maintenance needs and make adjustments as soon as they are needed. For example, tracking the number of cycles lets you know instantly when it’s time to replace a vacuum tube or suction cup with a lifespan of 10,000 cycles. Some cobots with “smart” sensors can even self-adjust based on collected data.
Many machines also collect data about when they’re running, which program is in use, errors, collisions, variations in speed or wait time, and more. The data is housed on your LAN or in the cloud, so you can pull this information into KPI reports in real time. It’s a great way to quantify the benefits of how a cobot is performing compared to a manual process. It’s also helpful for identifying further tweaks to processes such as movements, speeds, other aspects of the task.
While collecting and manipulating data aids decision-making, connectivity requires data security. To safeguard sensitive information, production data, and logic and behavior programming, following best practices is critical. Cyber risks and threats to manufacturing equipment are often new to small and medium companies just starting out with computerized automation. It pays to protect yourself and your facility.
Now and in the Future: The State of the Art
Artificial intelligence and computer algorithms frequently make the news, self-driving cars are inching closer to reality, and “lights out” manufacturing with no human workers isn’t just a sci-fi concept anymore. It might leave you wondering exactly what’s possible (or not) right now. The future is exciting but wide-scale implementation of much of the most extreme technology remains in the future (or at least in the lab).
“The most important difference that AI brings to robotics is enabling a move away from automation (hard-programmed) to true autonomy (self-directed). You don’t really see the difference if the robot only does one thing. But when the robot needs to handle several tasks, or respond to humans or changes in the environment, it needs certain levels of autonomy,” notes Robotics Business Review. As an example of how AI plays out in just one common application, here’s how AI might drive the evolution of robotic object handling in the near future:
- “Grasping an object, for example, without pre-determined locations and motions would be impossible without machine vision capable of reconstructing a 3D image, and AI to translate this visual information into a successful action on the part of the robot,” explains the Robotic Industries Association.
- “Tomorrow’s handling solutions will act more independently. The market is already demanding gripping systems that are quick and easy to set up and that automatically adapt to varying gripping situations,” says Dr. Markus Gluck of SCHUNK in an Advanced Manufacturing
Cobots In Action
Considering all of the features, capabilities, tooling options, and benefits to business and employee, what can a cobot accomplish in a small or medium size manufacturing setting?
No two cases are identical, but this example of a collaborative ultrasonic welding operation at an automotive parts supplier illustrates many of the benefits:
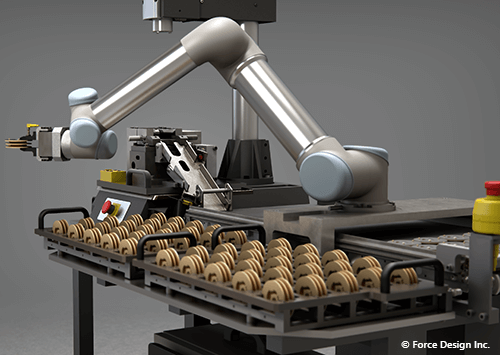
Before: A worker manually assembled four components and placed them into a fixture on an ultrasonic welder. After the manually initiated weld cycle was finished, the operator unloaded the completed assembly. A worker could make 100 assemblies per hour, but it was a constant struggle to achieve this level of production. The poor ergonomics of the equipment was causing fatigue and physical discomfort.
After: A worker still manually builds the assemblies, but now loads them into one of three staging pallets. Pallets are loaded off-line and placed onto the machine as needed. A collaborative robot equipped with a gripper transfers the assemblies from the pallets to an automated fixture on the ultrasonic welder. After the automatic weld cycle is complete, the fixture ejects the completed assemblies onto a conveyor which presents them to the operator for inspection and packaging. Sensors throughout the equipment verify presence of components and physical features ensure correct orientation and position.
Outcomes:
- output more than doubled from a barely achievable 100 per hour to a comfortable 210 per hour
- collaborative robot reduced physical workload while maintaining a safe environment
- operators experience less fatigue and discomfort
- operators enjoy working with the automation equipment
- while cobot is sharing the workload, operator is free to perform additional tasks
- equipment is designed to accommodate future variations of product with minimal changes
Fitting In: Finding the Right Place for a Cobot in Your Facility
Your workers have probably already thought “I wish I had a machine that could do this task for me.” If you haven’t already heard these musings from them, just ask. They’ll probably be able to come up with a few ideas for making their work less tedious, physically demanding, or more fulfilling.
Observe your process with an eye for what can be automated – online videos and robot vendor websites are a great way to see cobots in action and get a sense of all the things they can do. Can you picture it in your building alongside your employees? Brainstorm and have fun imagining what could be, such as:
- assembling pieces then rotating them into position for a worker to complete the job
- opening the door to a CNC machine, inserting an unfinished piece of material, closing the door, and repeating the process to remove it after machining
- inserting or removing items from the appropriate tray or rack based on simple logic programming
- tending an injection molding machine, opening and removing the part, pressing the start button, then trimming the new part while the next is molded.
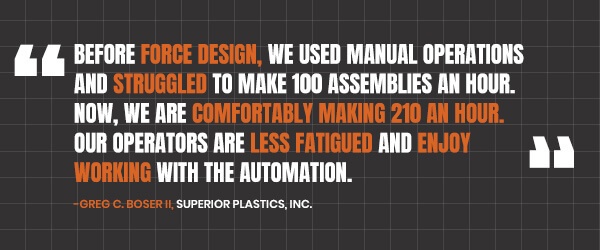
If adding automation equipment in your facility seems overwhelming or too complicated to implement, a cobot may be the perfect first step. They’re cost effective, easy to set up and operate, and probably won’t demand a complete overhaul of your manufacturing process (although they could be the catalyst to updating and automating more and more of it over time). The first step is examining your work cells and equipment for single tasks and applications that might translate to collaboration with a small robot. Sometimes all it takes is walking through the steps, picturing what a cobot would look like in place. Sometimes, it takes an experienced partner to get started. If you would like help exploring options, just let us know.