The skills gap is a hot topic in many industries, especially manufacturing. It’s created when the number of open jobs grows but there aren’t enough job seekers with the right skills to fill them. Research by Deloitte and the Manufacturing Institute says “the number of new jobs in manufacturing [will] accelerate and grow by 1.96 million workers by 2028.” However, the World Economic Forum (WEF) notes that 54 percent of workers will require significant reskilling or upskilling by 2022.
Manufacturers suffer if they can’t fill positions or are unable to prepare their existing workers for job changes. A big reason for this is the growing number of tasks previously performed by people that have become automated due to advanced computing and artificial intelligence. Examples include computer software that can operate machines and tools, or sensors and robotic “fingers” that can identify and move objects. As a result, fewer workers are needed for manual and repetitive tasks, and more jobs require programming or other computer expertise. And those whose jobs have been eliminated often don’t have the skills to adapt.
The impact on production includes:
- Reduced output due to limited staff or outdated equipment
- Missed market opportunities due to the inability to quickly scale up production or modify product offerings
- New product development suffers due to insufficient design staff or inability to analyze data on market needs
- A less competitive position in the global market due to limited capacity
What’s Causing the Mismatch?
The shortage of workers is partly due to retiring baby boomers, Millennials and Generation Z students entering the workforce later, and generally low unemployment rates. Employees are also feeling empowered by the strong economy to leave their jobs at higher rates (2.3 percent in November 2018, the highest since 2011) in search of higher wages and better benefits. As a result, the applicant pool is smaller overall.
But the very nature of work is also shifting, and that is the larger problem: many people just don’t have the education or skills to keep up. In manufacturing key factors in the change include artificial intelligence, automation, the Industrial Internet of Things, Industry 4.0, robotics, and data-driven decision making.
“The very nature of work is shifting, and that is the larger problem: many people just don’t have the education or skills to keep up.” Click to Tweet
Some jobs will be transformed more than others, so instead of looking at how an entire job will change or be eliminated, consider the effect of technology and automation on the constituent tasks of a job. This means that human workers are still required, but the daily work they do (often with more technology) and numbers of employees needed (often far fewer) for the work is different. For example, sheet metal fabricators will still be needed, but the task of positioning blanks in a press brake might be carried out by a machine. For a worker in this situation, retraining him or her to program and use the new equipment means they can adapt to the new skills and tasks required and keep their job.
More Education, Less Time
“The current educational requirements of the occupations that may grow are higher than those for the jobs displaced by automation,” reports a McKinsey article on the future of work. Research indicates that automation and technology advances will create demand for engineering, programming, data analysis, and other high-tech areas – things usually acquired through higher education or other intensive training. This training often costs more time and money than many low- and moderate-skilled workers can afford, especially those at mid-career.
It’s also predicted that companies will focus on retraining and upskilling their highest performing and highest skilled workers, potentially leaving low and minimally-skilled employees with even fewer options. WEF research shows that among many corporations, the “key success metric for reskilling and upskilling initiatives is increased workforce productivity [and] significantly smaller proportions of companies regard reskilling as a means of lowering recruitment costs, redeploying employees in disrupted job roles or as a way to increase the skills base of their medium- and lower-skilled workforce.”
The changes are coming fast too. WEF estimates that in 2018, 71 percent of work tasks were performed by humans and 29 percent by machines. By 2022, they predict 58 percent by humans and 42 percent by machines. “The task … will likely be to retrain and redeploy tens of millions of mid career, middle-age workers.” Simply put, jobs will change quickly enough to impact today’s workers, not just future generations.
“Jobs will change quickly enough to impact today’s workers, not just future generations.” Click to Tweet
What can companies do?
“As an employer, retraining your current talent to meet the needs of the demand works better with your bottom line than hiring a completely new workforce of talent from the bottom up,” writes Daniel Newman in Forbes. Bridging the skills gap is difficult, but there are things manufacturers can do to stay productive and cover staffing needs:
- Reskill/upskill current employees. Workers need to learn to use their day-to-day equipment, but the prevalence of computers and connected “smart” equipment also means they need to be comfortable with the technology in general. According to Deloitte, manufacturing executives prioritize technology/computer skills, digital skills, programming skills for robots/automation, working with tools and technology, and critical thinking skills.
- Build a culture of continuous learning. Take advantage of any training provided by automation equipment suppliers and encourage employees to ask questions and help each other. Access to training materials at the point of need and chat technology at workstations let workers ask questions and get answers quickly.
- Consider rehiring former employees or those returning to work after a leave of absence. Past experienced employees are often faster and easier to onboard and bring up to speed. If current employees leave, let them know that they are welcome to reapply in the future.
- Gather and share institutional knowledge. With millions of Baby Boomers heading for retirement, mentoring programs are a way for long-time employees to pass what they’ve learned over the years to incoming employees, especially in terms of critical thinking, problem solving, teamwork, and other soft skills that take time and experience to develop. You can also pair younger, tech-savvy workers with senior employees to share computer and technology skills.
- Retain more employees by supporting them. Training is crucial, but employees also rely on living wages, solid benefits, and other signs that their company looks at them as whole persons. As the job market tightens, your ability to differentiate yourself and provide what workers need matters. Things like flexible hours, job sharing, remote work, student loan assistance, and generous paid time off make a big difference in the current job candidate’s market.
- Support efforts to spread the message about manufacturing as a rewarding career. Opening your facility to middle and high school career programs and college students are all ways to show what modern manufacturing looks like. Internships and apprenticeships are great was to give students experience. Programs like Dream It Do It and manufacturing summer camp programs are examples of initiatives companies can support to fight the outdated notion of manufacturing many people have.
There’s no denying automation and technology are changing manufacturing. With a solid strategy, you can put it to work for your company and your employees. Force Design can help – please contact us today.
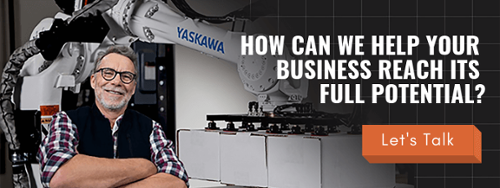