If you do a large amount of welding in your facility, you might wonder if automated welding is a good fit for your operations. That generally depends on your objectives and goals for automation. They differ for every company, but usually encompass three primary areas: efficiency, quality, and workforce management.
In this blog, we’ll take a closer look at each of these as well as some top tips for success with automated welding.
1. Efficiency
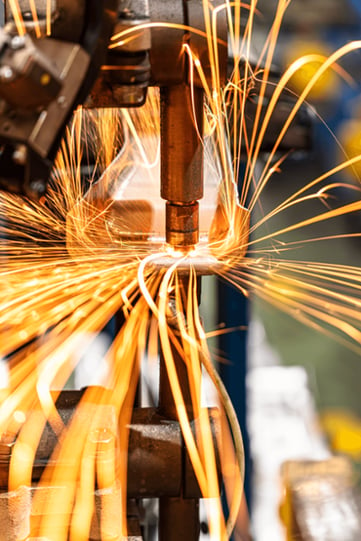
Some of the biggest gains from automated welding include shorter cycle times, increase throughput, and higher overall productivity.
These are due in large part to a robot’s high uptime and ability to operate continuously at the same rate of speed. Unlike humans, robots do not take breaks, vacation, or sick time. Additionally, robots do not succumb to distractions or fatigue and may even be able to run unattended for a period of time.
Quick-change tooling adds to productivity as well. Components can be barcoded or given a numeric code to input at the welding station, which in turn calls up the correct program and/or fixturing for the incoming part. This saves setup time and expands the number and type of welds that can be automated.
Another gain in efficiency comes from redistributing the workforce. For example, instead of focusing on simple, repetitive welds, people can be reassigned to welding tasks that aren’t easily automated, such as low-volume/high-mix, complex, or prototype work – all work that requires the thoughtfulness and skill of a person. In other cases, a single operator may be able to oversee multiple welding cells for increased productivity.
Finally, productivity and efficiency can get a boost by incorporating automation into tasks that precede and follow the welding cell. Examples include using conveyors or roller tables for infeed of components, adding a small robot to tend CNC machines upstream, and outputting finished parts directly to automated inspection stations equipped with cameras and sensors.
2. Quality
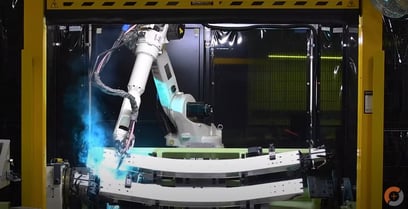
All welders have variations in their weld quality: no two welds are ever identical. Factors like fatigue, illness, poor ergonomics, hard-to-weld materials, or complex component geometries challenge even the best welders.
Automated welding systems, in contrast, produce high-quality, consistent outputs, but only when certain criteria are met:
- Properly prepped components (whether via CNC machining or manual processes)
- Inputs made to tolerance with minimal variability
- Careful programming
- Thorough debugging
The inherent repeatability of robotic welding equipment means that once the factors that influence quality (optimal parameters, fixtures, and motions) are set, they will be performed the same way, cycle after cycle.
In automated welding, quality is a cumulative concept – what happens upstream impacts the preparation and condition of components when they reach the weld station. Unlike a human welder, a robot can’t make up for part variability with fine on-the-fly adjustments (unless it is working on seams, in which case it can use laser seam tracking or touch sensing technology to find variability). Therefore, if out-of-tolerance or inconsistent components are welded by a robot, quality of the weldment and the resulting assembly and final product will probably be compromised.
Can Cobots Weld? Learn More in our Blog
3. Workforce Management
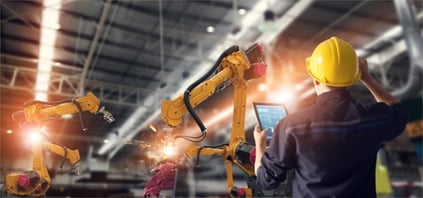
Consider this common scenario: someone mentions automating a manufacturing process, such as welding, and there is a subtle exchange of glances around the room, maybe some fidgeting in chairs, too. The unspoken question may very well be, “will automated welding take jobs away?”
While it may be possible to replace some jobs with robotic equipment, what we see more often is that automation changes the nature of human work. Welders and operators are still needed, but what they do from day to day is different.
Once a welding cell comes online, the welder’s primary role shifts to maintaining the flow of parts and keeping the machine running. Depending on the system, this may include loading and unloading pallets or trays, engaging or swapping out fixtures, or overseeing the entire welding system. But they still need to understand the welding process and have the ability to identify and troubleshoot defects.
Importantly, many companies are using robots to address the ongoing shortage of welders. In fact, the American Welding Society’s Careers in Welding website notes, “For every four Baby Boomers leaving the skilled trades only one Millennial enters.” In light of this, robotic welding cells can help manufacturers make the most of limited human resources by eliminating some of the jobs that were going unfilled and creating backlog and bottlenecks, anyway.
Robotic welding can also provide a measure of “age-proofing” by lessening the physical demands of welding work, thus enabling older welders to continue working past typical retirement age.
Tips for Success with Automated Welding
Keep in mind it’s not as simple as dropping a robot with a torch where a welder once stood. Some processes may have a one-to-one conversion to automation, but usually it’s necessary to alter the process to some extent to get an optimal outcome.
These tips will help you get the most from your welding automation project:
- To achieve consistent quality, robots require minimal variability of incoming components and careful fixture design.
- Experienced welders are needed to oversee the process, troubleshoot, and make adjustments.
- For the best outcome, be willing to invest time to get the system set up and debugged.
- Focus on automating the welding tasks that are high volume, error prone, tedious, or physically challenging.
- For enhanced value, consider integrating the welding system into other nearby processes like CNC machining or inspection.
- Keep welders and operators in the loop so they understand operational goals and how their roles will change.
- Prioritize the safety of welders, operators, and others working in the weld cell and in the vicinity.
- Work with a robotic welding integrator who is familiar with welding and fixture design, as well as robotics.
Read more about these and other aspects of welding system and fixture design, or contact the experts at Force Design to discuss your goals for automated welding.